|
With more than half of the equipment in process facilities consisting of motor-pump machine trains, it stands to reason that careful monitoring of these assets can prevent profit loss due to unplanned downtime. The CSI 9210 collects data from various sensor inputs and assesses the health of the motor-pump machine train. This assessment is based on an analysis engine that is specifically optimized for the particular machine train. Motor-pump combinations are the backbone of most industries. The processes that are driven by these
pumps are the life blood of the plant.
The CSI 9210 provides an optimized solution for easy device implementation as the data collection logic and the data analysis logic are factory configured. They are based on the specific needs of motor-pump combinations typically found in process industries.
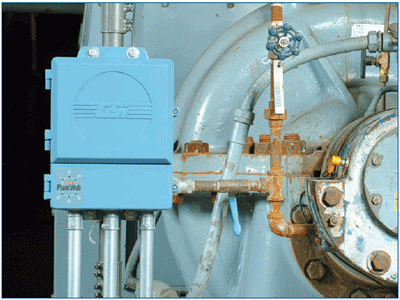 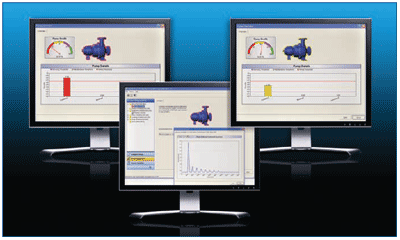
EDDL capabilities provide a more intuitive graphical interface and a common look and feel with other diagnostic instruments.
The CSI 9210 Machinery Health Transmitter collects data from various sensor
inputs and assesses the health of the motor-pump machine train.
Integration with CSI 2130 Extends the Reach of your Vibration Analysis Program
The most important aspect of the CSI 9210 is the production of results and the creation of information to optimize the operation of these vital motorpump rotating assets. Upon an alert condition, rich spectral data will be stored in the CSI 9210. With the 9200 Link application,the CSI 2130 Machinery Health Analyzer can be used to retrieve high-resolution spectral vibration and PeakVue? data from the CSI 9210. The data, once retrieved by the CSI 2130, can then be placed in a job format and stored in AMS Suite: Machinery Health
Manager for detailed analysis. The 9200 Link application allows you to truly extend the reach of your vibration analysis program.
Focused on the Needs of Both Operations and Maintenence
Operations and Maintenance have unique responsibilities within the plant which can impact the health of rotating equipment. Operations
is responsible for the production process and schedule, which sometimes means allowing machinery to operate outside of optimum set points. In the meantime, Maintenance is responsible for delivering uptime and avoiding unplanned production downtime. The CSI 9210 provides analysis results that help both of these functions achieve their goals. Alerts are routed through the plant’s process automation system to the operators’ workstations,helping them to understand how changes in operating set points postively and negatively impact
machinery health. Alerts are also routed to Maintenance workstations, where machine problems can be studied in depth and necessary repairs can be scheduled.
Specifications |
Sensor Input Details |
• Accelerometer AC-input channels have an input range of 10 Volts peak or 20 Volts peak-peak. For an accelerometer
with 0.1 V/g, the allowable input voltage corresponds to 70 g's RMS or 100g's Peak.
• Sensor power for each accelerometers channel is ~22VDC @ ~3 mA.
• Four temperature inputs for 10K-ohm thermistor sensors can measure from -40?C to 150?C. |
Data Conversion |
• All vibration input channels are collected simultaneously using 24 bit Sigma Delta ADCs which provide >120dB of dynamic range. The sampling rate of 102.4 kHz provides >40 kHz bandwidth. |
Signal Processing Requirement |
• Each AC-input channel has a frequency response of 1 Hz to 40 kHz.
• Each AC-input channel has a 105 dB minimum amplitude dynamic range. |
Memory for AC Channels |
• 64 MB is available for channel acquisition buffers.
• 128 MB of RAM is available for firmware, logic tables, temporary data storage, intermediate results, communcations buffers and historical data accumulation |
Environmental |
• Ambient temperature range is from -25?C to 60?C.
• Humidity limits are 0-95% relative humidity (non-condensing) and 0-100% relative humidity (non-condensing). |
Outputs |
Four Machinery Health Values:
• Overall Health
• Motor Health
• Coupling Health |
One Rotating Shaft Speed Six Temperatures:
• Ambient Temperature
• Motor Surface Temperature
• Auxillary Temperature 1
• Auxillary Temperature 2
• Enclosure Temperature
• Termination Panel Temperature |
Diagnostic analysis results via PlantWeb Alerts:
• Advisory
• Maintenance
• Failed |
Power Requirements |
External 24VDC power with 1 Amp capacity (24 Watts)
Device consumes approximately 10-12 Watts. |
Communications Requirements |
2-wire connection to FOUNDATION fieldbus |
Sensor Inputs to Device |
Eight Analog AC signal input channels:
• 1 Flux input
• 1 Tachometer input
• 6 Accelerometer inputs |
Six Analog DC temperature input channels:
• 4 External Temperatures
• 2 Internal Temperatures |
|